TPY
TPY waterproofing membrane 4 or 5 mm thick, is most suitable for use in TROPICAL areas.
TPY membranes are manufactured from bitumen, modified with atactic polypropylene (APP). The compound is a mixture of distilled bitumen, thermoplastic polymers, and elastoplastic copolymer which gives the membrane excellent durability and flexibility at low temperature -12°C, and the ability to withstand high temperatures.
The reinforcement is 200g/m² non-woven polyester fabric to give about 45-50% elongation and provide the membrane with the required resistance to heat aging, puncture and rotting.
TPY is manufactured with a polyethylene film on the lower face to prevent sticking in the roll and which melts quickly when subjected to heat during installation, and gives a visual sign of the correct melting temperature of the membrane. The upper face is covered with fine sand, granule, or colored slates when the membrane is used as the exposed top layer.
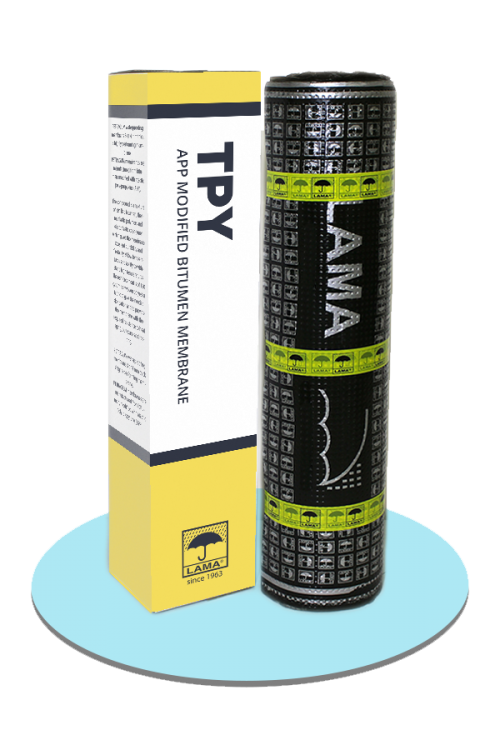
Key Features.
- Single-ply waterproofing layer.
- Fast, easy and clean application.
- Can be applied to repair existing asphalt roofing systems.
- Highly resistant to weathering.
- Resistant to salt solutions, dilute acids and alkalis.
- Resistant to U. V.
Packaging Information.
- Dimension: 1×10 m/roll
- Thickness: 4 or 5 mm
- Weight per roll: 50 or 62 Kg
- Reinforcement: Nonwoven Polyester 200g/m²
Application Field.
Due to its excellent resistance and elongation, TPY is used for a wide range of waterproofing applications such as:
- Roofs (reinforced concrete, prefabricated concrete, metal and timber deck).
- Roof gardens, terraces, kitchens, bathrooms, etc.
- Underground foundations, basements, and retaining walls.
- Reservoirs, basins and canals.
Application Method.
- Lay down the rolls so that the lower face with polyethylene film is bonded to the substrate.
- To fix the sheet to the substrate, use a propane gas burner to melt off the polyethylene film and a thin layer of bitumen while unrolling and laying the membrane.
- Seams at overlaps should be properly secured and smoothed on with a hot round-tipped trowel.
- The side lap is 100mm and the end lap is 150mm.
- The membrane may be loosely laid, partially or fully bonded, depending on the structure and the specifications.